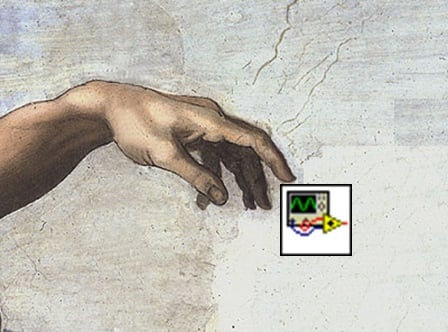
Digital transformation is revolutionizing industries worldwide, improving operational efficiency, enhancing productivity, and providing opportunities for competitive advantage. In an evolving technological landscape that requires businesses to navigate complex marketplaces, digital transformation not only empowers businesses, but also helps them to navigate common pain points that crop up across industries.
At DSA, we leverage digital transformation to improve low labor productivity and cut high labor costs, enhance production and test capacities, elevate product quality, and provide better data visibility across operations while navigating internal and external pressures. In solving these challenges, we help businesses accelerate their time-to-market while adhering to regulatory compliance.
We leverage digital transformation to help you solve these common pain points across industries, including manufacturing, energy, healthcare, government, consumer electronics, transportation, and more!
Page Contents:
1. How To Improve Labor Productivity and Cut High Labor Costs Using Digital Transformation
2. Improving Production Capacity, Test Capacity, Product Quality & Data Visibility Across Your Operation With Digital Transformation
3. How Digital Transformation Improves Time-to-Market Value
4. Internal and External Operational Challenges That Impact Your Bottom Line, and How to Resolve Them with Digital Transformation
SECTION 1
How To Improve Labor Productivity and Cut High Labor Costs Using Digital Transformation
What is labor productivity and how is it calculated?
Higher labor productivity means more is produced in less time, indicating efficient use of labor resources.
Labor productivity is typically calculated as the total output per labor hour. Several factors can influence your operation’s labor productivity:
Technology: Advanced technologies can streamline processes and increase output.
Skills and Education: A more skilled workforce can perform tasks more efficiently.
Capital Investment: Investments in machinery, equipment, and infrastructure can enhance productivity.
Management Practices: Effective management strategies can optimize workflow and reduce waste.
How to calculate labor productivity
1. Calculate output value
Measure the value of the product or service produced over a period of time.
2. Calculate labor time
Calculate the total number of hours worked by employees over the same period of time.
3. Calculate labor productivity
Divide the output by the labor to calculate labor productivity for the period.
For example, if a company produces $80,000 worth of goods or services in 1,500 labor hours, the labor productivity is $53 per hour ($80,000 /1,500).
What is the relationship between labor costs and labor productivity?
The relationship between labor costs and labor productivity is crucial for maintaining profitability, controlling inflation, and ensuring businesses stay competitive. Higher productivity can offset rising labor costs, while stagnant productivity with rising labor costs can lead to economic challenges.
Compelling labor productivity & labor cost statistics
Compensation Increase: Compensation costs for civilian workers rose by 0.9% from September to December 2024. Over the year ending in December 2024, total compensation increased by 3.8%, with wages and salaries also rising by 3.8%, and benefit costs by 3.6%. – Bureau of Labor Statistics
Unit Labor Costs: In the fourth quarter of 2024, unit labor costs in the nonfarm business sector increased by 3.0%, reflecting a 4.2% rise in hourly compensation and a 1.2% increase in productivity. Over the last four quarters, unit labor costs went up by 2.7%. – Bureau of Labor Statistics
Manufacturing Sector: Unit labor costs in the manufacturing sector increased by 3.3% in the fourth quarter of 2024, with a 4.1% rise in hourly compensation and a 0.8% increase in productivity. From the same quarter a year ago, manufacturing unit labor costs increased by 1.5%. – Bureau of Labor Statistics
Mitigating High Labor Costs with Digital Transformation
5 signs of low labor productivity
Low labor productivity can be measured both qualitatively and quantitatively. In addition to output not meeting expectations, you may feel friction in your team prior to identifying inefficient software or processes that prevent operations from running smoothly. The following signs can indicate low labor productivity:
- Declining Output Per Employee: If your team’s output isn’t growing in proportion to the resources invested, productivity is lagging.
- High Operational Costs: Rising labor costs without a corresponding increase in efficiency often signal a problem.
- Excessive Overtime & Burnout: If employees frequently work extra hours to meet goals, processes may be inefficient.
- Inconsistent Quality & High Error Rates: Poor productivity often leads to mistakes, rework, and inconsistent quality.
- Slow Time-to-Market: Delays in production, service delivery, or decision-making suggest bottlenecks in workflows.
Mitigating Low Labor Productivity with Digital Transformation
How digital transformation improves productivity and decreases labor costs
Automation frees people from the drudgery and repetition of performing a task over and over. It provides a consistency that cannot be matched by humans, whether it’s taking a reading, assembling a unit, or even checking the appearance of a finished product. It can pass information smoothly into records for either real-time awareness or post-processing analysis. With the proper architecture, the automation is easy to adapt to new measurements or tests for continual process improvement, including:
Robotics: Machines that can perform repetitive or complex tasks with high precision.
Artificial Intelligence (AI): Systems that can analyze data, make decisions, and improve over time.
Software Automation: Programs that can handle administrative tasks, data entry, and other routine processes.
At DSA, it is our mission to leverage automation to improve labor productivity and cut labor costs for your business. We achieve this through implementing the following types of automation:
Laboratory Automation
Product Automation
Manufacturing Automation
Test Automation
FAQs about labor productivity
Q: Will automation lead to massive unemployment?
A: While automation can displace certain jobs, it also creates new opportunities in tech development, maintenance, and other areas. With proper support and retraining programs, the transition can be managed effectively.
Q: How can small businesses afford automation?
A: Small businesses can start with cost-effective automation solutions and gradually scale up. There are also various grants and financing options available to support automation initiatives.
Q: What skills will be in demand in an automated world?
A: Skills in technology, engineering, data analysis, and problem-solving will be increasingly valuable. Soft skills like adaptability and continuous learning will also be important.
SECTION 2
Improving Production Capacity, Test Capacity, Product Quality & Data Visibility Across Your Operation With Digital Transformation
How do production capacity, test capacity, product quality & data visibility contribute to business efficiency, profitability, and sustainability?
In today’s competitive market, improving production capacity, test capacity, product quality, and data visibility are critical for any operation aiming for excellence. These elements are interconnected and collectively contribute to the overall efficiency, profitability, and sustainability of a business.
Improving Production Capacity with Digital Transformation
Compelling production & test capacity, product quality & data visibility statistics
Production Capacity & Automation:
Companies that implement smart manufacturing technologies see up to a 25% increase in production capacity.
– McKinsey
Testing Efficiency:
Automated testing systems reduce testing times by 30-50%, improving throughput and reliability. – Gartner
Product Quality & Costs:
Improving product quality reduces warranty and defect costs by 15-25% while increasing customer retention rates.
– Forbes
Data-Driven Decision-Making:
Businesses that leverage real-time data analytics experience a 20% boost in overall efficiency. – Deloitte
Improving Test Capacity with Digital Transformation
Signs your business has operational inefficiencies such as
low production & test capacity, product quality, and data visibility
Production capacity, test capacity, product quality, and data visibility are essential to keep your business running smoothly. You must be able to produce your product as efficiently and error-free as possible, ensure adequate testing and quality assurance, as well as have insight into each stage of production. The following signs can indicate poor capacity, quality, and insight into your production.
Signs of Low Production Capacity
- Frequent production delays and bottlenecks.
- Increased lead times for orders.
- High machine downtime due to maintenance issues.
- Inability to scale operations effectively.
Signs of Poor Test Capacity
- Slow testing processes causing delays in product release.
- High rates of defective products making it to market.
- Over-reliance on manual testing methods.
- Compliance issues due to inadequate testing procedures.
Signs of Poor Product Quality
- Frequent product recalls or high return rates.
- Negative customer feedback regarding reliability or performance.
- High costs associated with rework and warranty claims.
- Inconsistent quality control across different production batches.
Signs of Low Data Visibility
- Difficulty accessing real-time production and operational data.
- Siloed information across departments leading to poor collaboration.
- Inability to track key performance indicators (KPIs) effectively.
- Decision-making based on outdated or incomplete data.
Improving Low Data Visibility with Digital Transformation
How digital transformation helps improve production capacity, test capacity, product quality, and data visibility
Production capacity, test capacity, product quality, and data visibility are essential to keep your business running smoothly, and digital transformation ensures that you have capacity to support consistent production with quality output that is representative of your business, as well as visibility into data that will help you continuously improve your operation and make it more efficient.
Improving Production Capacity
-
Automation & Robotics: Streamline repetitive tasks and improve efficiency.
-
Predictive Maintenance: Uses IoT sensors to reduce downtime and increase machine longevity.
-
Lean Manufacturing Principles: Identify and eliminate waste to maximize production efficiency.
Improving Test Capacity
-
Automated Testing Systems: Reduce manual intervention and enhance accuracy.
-
AI-Driven Quality Control: Uses machine learning to detect defects faster.
-
Data-Integrated Testing Environments: Real-time analytics for better decision-making.
Improving Product Quality
-
Quality Management Systems (QMS): Ensure adherence to industry standards.
-
Supplier Quality Control: Vet materials to ensure high standards from the start.
-
Continuous Improvement Strategies: Implement Six Sigma and lean methodologies.
Improving Data Visibility
-
Cloud-Based ERP Systems: Provide centralized data access across departments.
-
Real-Time Analytics & Dashboards: Enable proactive decision-making.
-
AI & Machine Learning Insights: Predict trends and optimize operations accordingly.
Improving Product Quality with Digital Transformation
FAQs
Q: What’s the first step to improving production capacity?
A: Conduct an operational audit to identify inefficiencies and bottlenecks, then prioritize automation and process optimization.
Q: How do I balance high production output with quality assurance?
A: Implement robust quality management systems and use automated inspection tools to maintain standards while increasing output.
At DSA, it is our mission to leverage automation to improve production capacity, test capacity, product quality, and data visibility. We achieve this through implementing the following types of automation:
Laboratory Automation
Product Automation
Manufacturing Automation
Test Automation
SECTION 3
How Digital Transformation Improves Time-to-Market Value
How automation improves time-to-market speed
Companies are under increasing pressure to deliver products and services quickly while maintaining quality and innovation, with production speed being the most critical factor in successfully achieving this goal. Automation plays a key role in accelerating time-to-market by streamlining workflows, reducing manual processes, and improving operational efficiency.
Prevent Missed Time-to-Market Deadlines with Digital Transformation
Understanding time-to-market value
Time-to-market (TTM) refers to the period it takes from a product being conceived until its availability for sale. Faster TTM can provide a competitive advantage, but several challenges can slow down the process:
-
Development Delays: Bottlenecks in the product development lifecycle.
-
Testing and Quality Assurance: Ensuring product quality and safety without delays.
-
Coordination and Collaboration: Efficiently managing cross-functional teams and processes.
-
Regulatory Approvals: Navigating the regulatory approval process can be time-consuming.
Navigating Regulatory Compliance with Digital Transformation
How digital transformation decreases time-to-market
Digital transformation is essential for improving time-to-market by offering tools and technologies that streamline operations, boost communication, and automate processes. Here’s how:
- Workflow Automation: Reduces manual tasks, speeding up product development and ensuring resources are used efficiently.
- Predictive Analytics: Anticipates issues and helps businesses plan proactively, preventing delays and ensuring timely delivery.
- AI-Driven Knowledge Management: Captures and shares valuable insights across teams, minimizing knowledge gaps and accelerating decision-making.
- Cloud-Based Collaboration Tools: Enhances communication and coordination across teams, reducing bottlenecks and improving collaboration speed.
- Optimized Supply Chain Management: Reduces disruptions and ensures timely availability of materials, streamlining the development process.
By leveraging these digital solutions, businesses can cut down the time it takes to move from ideation to product release, remaining agile and responsive in an ever-evolving market. Digital transformation removes friction, accelerates growth, and helps companies capitalize on new opportunities faster.
Compelling time-to-market statics
Speed of Innovation:
56% of companies using digital transformation technologies report a significant improvement in product development speed, helping them launch products 20-25% faster than competitors. – PwC
Reduced Development Time:
Businesses that automate their workflows experience up to a 30% reduction in the time spent on manual processes, directly contributing to faster time-to-market. – McKinsey & Company
FAQs
Q: How long does it take to see results from digital transformation?
A: The timeline varies depending on the complexity of your business and the solutions you implement. However, many companies begin to see improvements in time-to-market within 6-12 months.
Q: Is digital transformation only for large enterprises?
A: Not at all. Small and mid-sized businesses can also leverage scalable and cost-effective digital solutions to improve efficiency and accelerate time-to-market.
Q: What are the most common obstacles to digital transformation?
A: Challenges often include upfront implementation costs, resistance to change, and the need for a solid cybersecurity strategy. With the right planning and support, these obstacles can be overcome.
SECTION 4
Internal and External Operational Challenges That Impact Your Bottom Line, and How to Resolve Them with Digital Transformation
How digital transformation helps stabilize threats posed by internal and external challenges
Businesses today face a range of operational challenges that can erode profitability and hinder growth. Internal challenges, such as resource constraints, tribal knowledge loss due to employee turnover, and inefficient processes can lead to operational inefficiencies. At the same time, external threats including supply chain dependencies, shifting market dynamics, and competitive pressures, can disrupt operations and negatively impact your bottom line. Digital transformation provides the tools and strategies necessary to mitigate these risks and drive sustainable growth.
Solving for Lost Tribal Knowledge with Digital Transformation
Operational inefficiency statistics:
Employee Turnover & Knowledge Loss:42% of employees say their companies lack a formal knowledge-sharing strategy, leading to inefficiencies and repeated mistakes. – Panopto
Operational Inefficiencies:
Inefficient internal processes cost businesses up to 20-30% of their annual revenue. – IDC Research
Break Dependencies on Suppliers with Digital Transformation
Signs your business needs to insource or outsource key operational processes, knowledge, or equipment.
If you're experiencing operational inefficiencies such as overburdened teams, loss of knowledge, supplier dependencies, and lagging behind competitors, it indicates poor production capacity, low product quality, and limited data visibility. You may be experiencing operational inefficiencies if you notice:
- Lack of Internal Resources: Teams are overburdened, leading to project delays and employee burnout.
- Loss of Tribal Knowledge: Critical knowledge leaves with employees, causing disruptions and inefficiencies.
- Dependence on Key Suppliers: A single supplier issue significantly impacts your ability to deliver products or services.
- Competitive Pressures: Competitors with stronger digital capabilities are gaining market share while your growth stagnates.
Circumventing Competitive Threats with Digital Transformation
How digital transformation helps streamline operations to preserve knowledge & strengthen supply chains.
Digital transformation enhances efficiency and competitiveness by automating tasks, preserving knowledge, strengthening supply chains, and improving data-driven decision-making to streamline operations and reduce inefficiencies.
Knowledge Retention & Workforce Efficiency
- Implement AI-powered knowledge management systems to capture and retain institutional knowledge.
- Automate repetitive tasks, freeing employees for higher-value work.
Supply Chain Resilience
- Use predictive analytics to anticipate and mitigate supplier disruptions.
- Diversify vendor relationships with real-time digital procurement tools.
Process Automation & Efficiency Gains
- Deploy workflow automation to streamline operations and reduce manual errors.
- Integrate cloud-based collaboration tools to improve cross-functional communication.
Competitive Advantage Through Innovation
- Leverage data analytics to drive smarter decision-making.
- Adopt digital customer engagement platforms to enhance client satisfaction.
Solving For a Lack of Internal Resources with Digital Transformation
FAQs
Q: How long does it take to implement digital transformation initiatives?
A: The timeline depends on the complexity of your business needs, but many companies begin seeing results within 6-12 months.
Q: Is digital transformation only for large enterprises?
A: No, small and mid-sized businesses can also benefit by implementing scalable and cost-effective digital solutions.
Q: What are the biggest risks of digital transformation?
A: Common risks include implementation costs, resistance to change, and cybersecurity threats. A clear strategy and stakeholder buy-in can mitigate these risks.
At DSA, it is our mission to leverage automation to circumnavigate internal and external pressures that threaten your business and prevent you from staying competitive.
What We Recommend
Get started today and schedule a free consultation. Try us risk-free and learn how you can benefit from our methodical and certified best practices to advance your automation engineering and digital transformation initiatives.